“We have to make sure we have the best quality and that we are putting in maximum effort, because we are the heartbeat, and without the heartbeat, Amerex doesn’t run. It’s just like the heart in a person. If you look at a person from the outside, you can’t see their heart, but you can feel it. When you do an X-ray, you can really see the heartbeat of the operation.”
Russell Chapman, Amerex Powder Manufacturing Supervisor
Russell couldn’t have said it any better about Amerex fire exginuisher powder. Simply put, without fire extinguisher powder there wouldn’t be a fire extinguisher. The Amerex powder manufacturing team has made its own proprietary powder formula since the 1970s. In the back of the plant, the team is quiet, but their motivation and dedication speak volumes. The 10-member crew of unsung heroes produce the powder, or the lifeblood of Amerex fire extinguishers. With seven team members on the day shift and three that rule the night, the team works together to make high-quality dry powder extinguishing agent in the safest manner possible.
Jeff Layfield, Senior Production Manager, has known the Amerex powdering manufacturing process almost since its inception. He began on the fire extinguisher assembly line in May 1977 and became the powder manufacturing supervisor in 1980. Fast forward 43 years later and he now overlooks all manufacturing plant operations while coordinating with other team members to streamline processes for consistency and efficiency. One of those team members is Russell, who has worked in powder manufacturing for the past seven years and now assumes the role of supervisor just as Jeff did. Leading the powder operations team, Russell is responsible for maintaining the powder supply and testing each batch of powder to make sure it meets regulations and specifications. The team has a wealth of experience in manufacturing this powder extinguishing agent that is so vital to Amerex fire extinguishers. Together, they have over 106 years of experience.
TYPES OF FIRE EXTINGUISHER POWDER:
- One of the most common extinguishing agents, ABC dry chemical powder is a general-purpose fire extinguishing chemical. Ninety percent of the hand portable fire extinguishers produced at the Amerex plant contain this powder.
- Rated for class B and C fires, Purple K powder knocks down flames caused by flammable liquids and electrical equipment or current.

THE PULSE OF FIRE EXTINGUISHER POWDER MANUFACTURING
The Amerex powder mills have expanded through the years. Today’s powder mills produce 10 times the amount of ABC and dry chemical powders per hour than was produced in 1977.
Since that time, two larger and more powerful mills were constructed to help increase production. The original mill was repurposed in the 1980s and is now used for Purple K powder only. It takes accountability and a lot of responsibility to maintain the mills today to make sure the company can produce the absolute best quality product. This steadfast dedication is how the company developed its motto that “Quality is behind the diamond.”
“It’s been important for Amerex to be able to manufacture our own powder, because it gives us the advantage of not depending on someone else to provide that for us,” Jeff says. “We can control the quality of it and make sure it’s up to the standards of what we do. Making powder is vital to our operations.” After production, the entire extinguisher undergoes rigorous testing by UL Solutions, including the powder formula. UL testing shows how fast the extinguisher discharges, what nozzle size it uses and the size of fire that can be extinguished with Amerex-manufactured powder. “You can’t put other powder in our fire extinguisher and expect the same performance,” Jeff explains. “It really voids the fire extinguisher if you do that. Each Amerex extinguisher is based on our powder.”
Currently, Amerex produces ABC powder that can be used in 2.5-, 5-, 10- and 20-pound handheld extinguishers and in our large wheeled units. The powder department keeps enough powder on hand for production by making millions of pounds of powder every month. The pound rating refers to the amount of powder inside the fire extinguisher, not the total weight. To accomplish that mammoth volume, the team needs plenty of raw materials, which come into the plant in a unique way. The bulk of the materials and chemicals are delivered via rail car or truck. From there, the material drops from the bottom of the rail car or the truck into an underground tunnel where a screw auger transports it to a bucket elevator and into the plant. At the top of the elevator, the material is discharged into a chute that leads to silos or tanks for storage. When the materials are ready to be used, a sorting turn head helps move the fire extinguisher powder where it is needed. This raw material yields enough to keep up with Amerex monthly extinguisher volume. And the quality of this powder lasts. “Everything that we ship out is 100 percent,” Russell says. “I know people who have older Amerex extinguishers, and they still fire off with no problem. If you shoot the powder onto the ground, it looks the same that it did when it was made years ago.”
While technology has changed allowing Amerex to evolve and upgrade our operations, the way the powder is ground and mixed has not changed over the years. The grinder and the mixer are integral to the powder production process. “We make the best in the business,” Russell says. “That’s probably why we’re the number one fire extinguishing plant in the world, because we really do work to live up to the slogan, ‘Quality is behind the Diamond.’ If you put all of your work into having the best quality, the product will speak for itself.”
The powder operators and team members in the powder room have great dedication and pride in their work. Training is critical—to ensure safety and the quality of the powder. “My biggest priority every day is to make sure everyone leaves the way they came in; that everyone is safe,” Russell says. “Along with making sure we have quality powder in the silos at all times.” Once the powder is finished, it is pumped to the product lines and into the extinguishers, which are then sent down the line for labels, valve assemblies, and brackets before they are packed into carton boxes and loaded onto pallets awaiting delivery to Amerex customers. “‘Quality is behind the Diamond’ has been around a long time,” Jeff says. “A diamond is one of the most precious gemstones—everyone wants one—and really it says that Amerex produces the gemstone of fire extinguishers. For me, it’s all of the people that work to make it a successful product, day in and day out. From the beginning to now, it has always been about the people. It’s a pleasure to work with all of these people.” From valve assembly to powder manufacturing to painting to maintenance to the front office, it’s the entire group working together that makes the difference. Every person that touches Amerex fire extinguishers is a quality inspector. It’s up to each person and the team to be responsible for quality.
“We have a product that is so well made and so well designed that as long as you do your job properly, it will be a quality product. It’s very important to maintain quality because we produce a life-saving tool. It has to work every time you use it. A lot of the time, fire extinguishers are used to save property, but the main thing is to save a life.”
Jeff Layfield, Senior Production Manager
PROTECTING LIFE
There are three elements to a fire: oxygen, heat, and a combustible material. If you can eliminate one, the fire goes out. When you spray ABC dry chemical powder on a fire, it removes the oxygen and coats the combustible material to form a protective barrier using a monoammonium phosphate base that blankets the area and melts over the fire to prevent reignition. “The powder on the inside—that’s what will save your life,” Russell says. Other fire extinguishing agents that Amerex produces are for specialty applications like around health care equipment or in computer labs or data centers.
THE HEARTBEAT OF THE OPERATION
The powder team works well together and motivates each other to be the best they can be and to produce the best quality powder. Russell makes sure to show each member his appreciation and highlights when they each stand out. The seasoned veterans on the team set the tone because they know the team is the “heartbeat of Amerex.” Newer members have soaked up information and training knowledge like a sponge, really showing their drive to uphold the quality that is behind Amerex products and everything the company does.
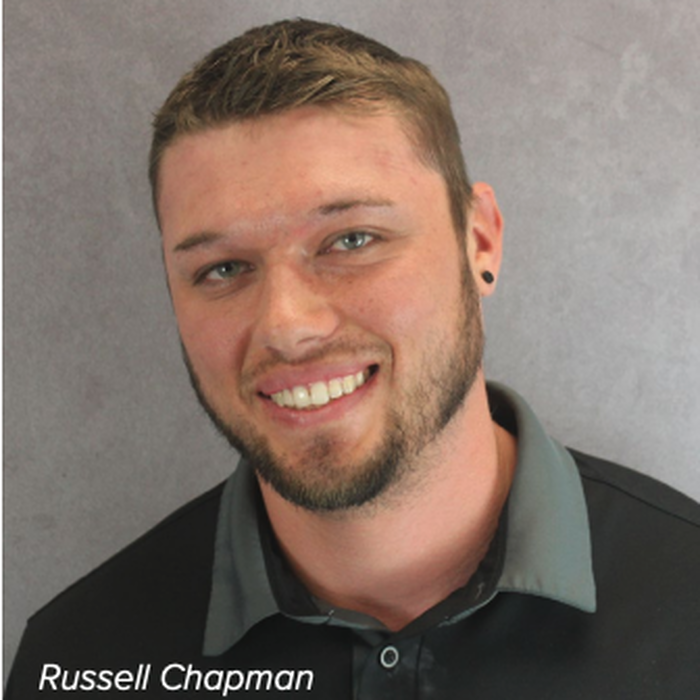
“My biggest priority every day is to make sure everyone leaves the way they came in; that everyone is safe, along with making sure we have quality powder in the silos at all times.”